Peter Paul Electronics Co., Inc., proud to announce ISO 9001 certification.
Peter Paul started formally implementing ISO 9000 in Y2005. Over a 5-1/2 year span, the companies operating processes were documented, and modified where necessary, to not only comply with ISO 9000 requirements, but to establish a robust Quality Management System (QMS). Importance was placed on efficiency and effective quality management system rather than have a certificate on the wall, so seeking certification was secondary.
The PeterPaul senior management team and the Mangiafico family supported the effort over the five and a half years. The “system” was implemented essentially in the background, invisible to the plant personnel. Internal audits were performed,
and improvements made. One key element in the implementation, was to marry the QMS to the Lean Transformation and 5S methodology PeterPaul was also implementing during the same period of time. The QMS documents the standard work developed using 5S methodology. The QMS is an integral part of the transformation instead of a standalone system and some companies choose.
A very tangible benefit of documenting the processes is that 1) processes are standardized, and 2) new personnel can be trained to the same standard process instead of relying on people’s memory and “tribal knowledge.” Review of the QMS was also integrated into company strategic planning and the progress reviewed.
The ISO-9000 standard requires 6 processes
that must be documented and controlled:
• Document Control
• Control of Quality Records
• Competence, Training and Awareness
• Control of Nonconforming Product
• Corrective Action
• Preventive Action
The training and education piece is important to achieve buy-in of all team members. A training presentation will now become part of the new employee orientation process. Training and training effectiveness are two key components that will be audited on each year. PeterPaul is in the process of developing an annual training plan plant-wide.
Approximately 25% of the employee population has been at the company in excess of ten years. To learn new tools and make significant changes to how tenured employees approach their work is commendable. And happily employees are actually more
satisfied since this effort. PeterPaul not only monitors internal metrics, but maintains a very comprehensive data driven process for analyzing customer returns to provide further process and product improvements. Suppliers are also monitored for performance in Quality, On-time Delivery and Responsiveness to PeterPaul needs.
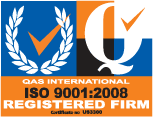